SWARCO - Pioneering Production Sustainability
In an era where sustainability and environmental protection are increasingly important, the development of sustainable high-performance, future-ready offerings for the human eye and beyond to our customers is on the daily agenda of SWARCO.
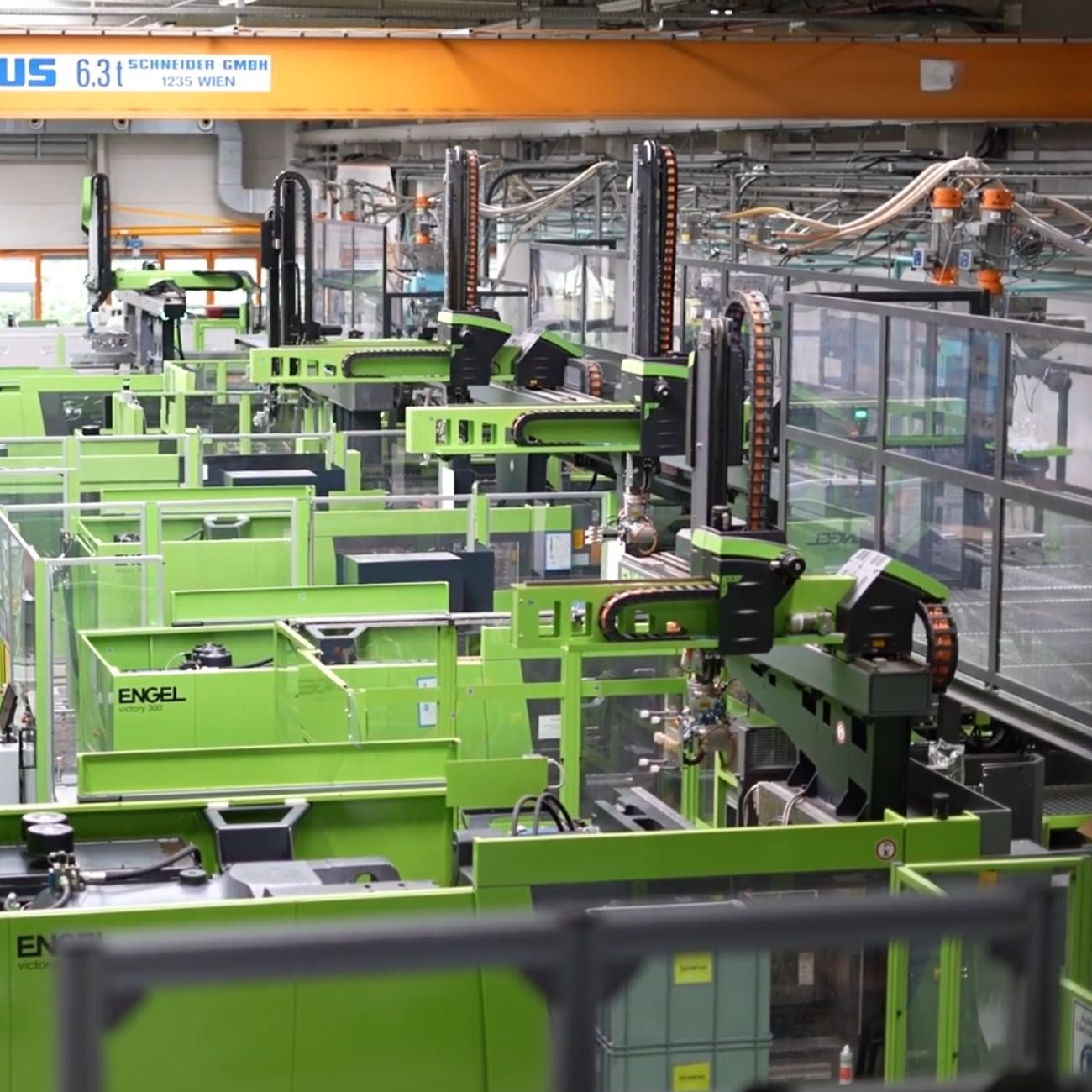
Being market-leader in Intelligent Transportation Systems and Road Marking Systems, advocating for green traffic management solutions is crucial to supporting cities from all around the world in meeting ambitious climate objectives (e.g. European Green Deal). No matter which products or solutions customers are asking for, they can be sure that helping them in improving their ecological footprint is one of our top priorities.
But that’s not the end of the story - as the trusted choice for future-ready mobility solutions, Corporate Social Responsibility (CSR) is firmly rooted in our mindset.
What does that mean?
Having a look at our production facilities, we demonstrate our integrity by producing our portfolio with respect to social values and environmental protection and align our commitment to sustainability with international standards to reinforce our credibility as a promoter of eco-friendly practices.
One of our frontrunners in this matter is our innovative production company SWARCO Futurit in Neutal (Burgenland), the world's largest traffic light producer and producer of SWARCO's Variable Message Signs (VMS). The factory has taken up the challenge and aims to become energy self-sufficient through the use of a photovoltaic system.
Of course, huge production volumes lead to a high energy demand. In this case we are talking about approximately 3 million kilowatt hours a year. Being aware of this, the question was raised on how to produce this amount of energy in a more environmentally friendly way, so SWARCO Futurit has opted on a photovoltaic system.
This system, installed between November 2023 and February 2024, was put into operation immediately after completion. With a total amount of 2.228 panels coupled to 9 inverters, it is capable of producing a peak of 914 kilowatts per hour in ideal circumstances. In as early as February, a month with very little hours of sunlight and a flat angle of solar radiation, it was possible to operate production energy self-sufficiently during parts of the day. These are ideal conditions for supplying our injection moulding machines, which are used to manufacture the plastic parts for traffic lights and signs, with green energy.
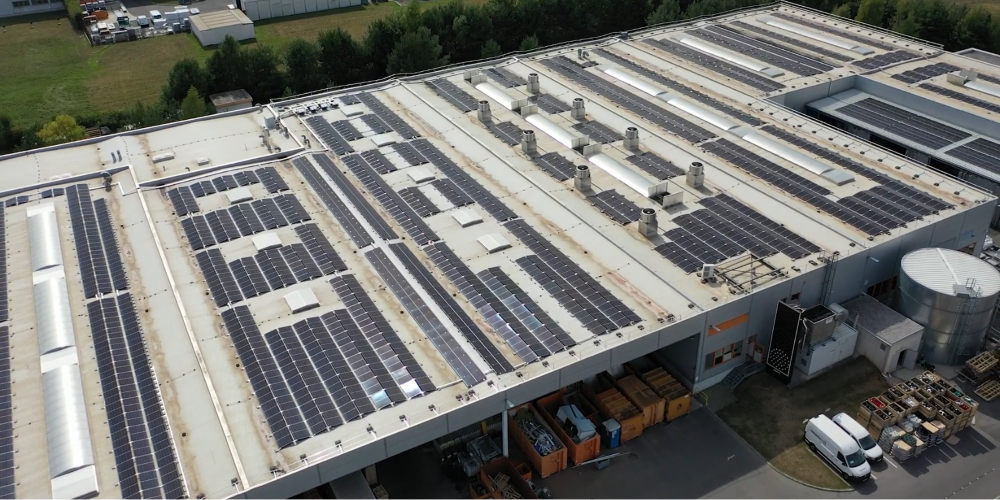
Using waste heat as an energy source
A special characteristic of energy is, that it is never really “consumed”. It is only converted into another form of energy and in the interests of sustainability, we want to take advantage of this. The photovoltaic system for example, converts light energy into electricity using solar cells to run the injection moulding machinery. During operation, a considerable amount of the electricity from the photovoltaic system is converted into kinetic energy in the hydraulic system, but not all of it – because these machines also produce a lot of heat in the hot runner mould. And that's exactly where we have applied the next lever: In order to prevent damage, these machines need coolants (in this case water). The waste heat generated is therefore absorbed by the water and fed into a heat pump, which then raises the temperature level even further and thus ensures the desired temperature for the heating water cycle. Instead of 12°C - 14°C from the water pipe, the heat pump works with the 30°C - 35°C cooling water. This is a significant energy saving because the rise to 40°C - 60°C required heating temperature is much more efficient. Although the heat pump also needs some electricity, the total savings in the factory are significant.
Having a look at the consumption of gas used for the heating of the buildings, the implementation of these measures reduced the need for this fossil energy source by more than 50 %, which is an important step forward towards a greener production.
In a time where climate change and environmental pollution pose global challenges, the production facilities of SWARCO Futurit in Neutal demonstrate that sustainable business is possible. Through the use of renewable energy and the implementation of sustainable production practices, we set the benchmark for environmentally conscious action in the industry and contribute to creating a greener future for generations to come.
SWARCO. The Better Way. Every Day.
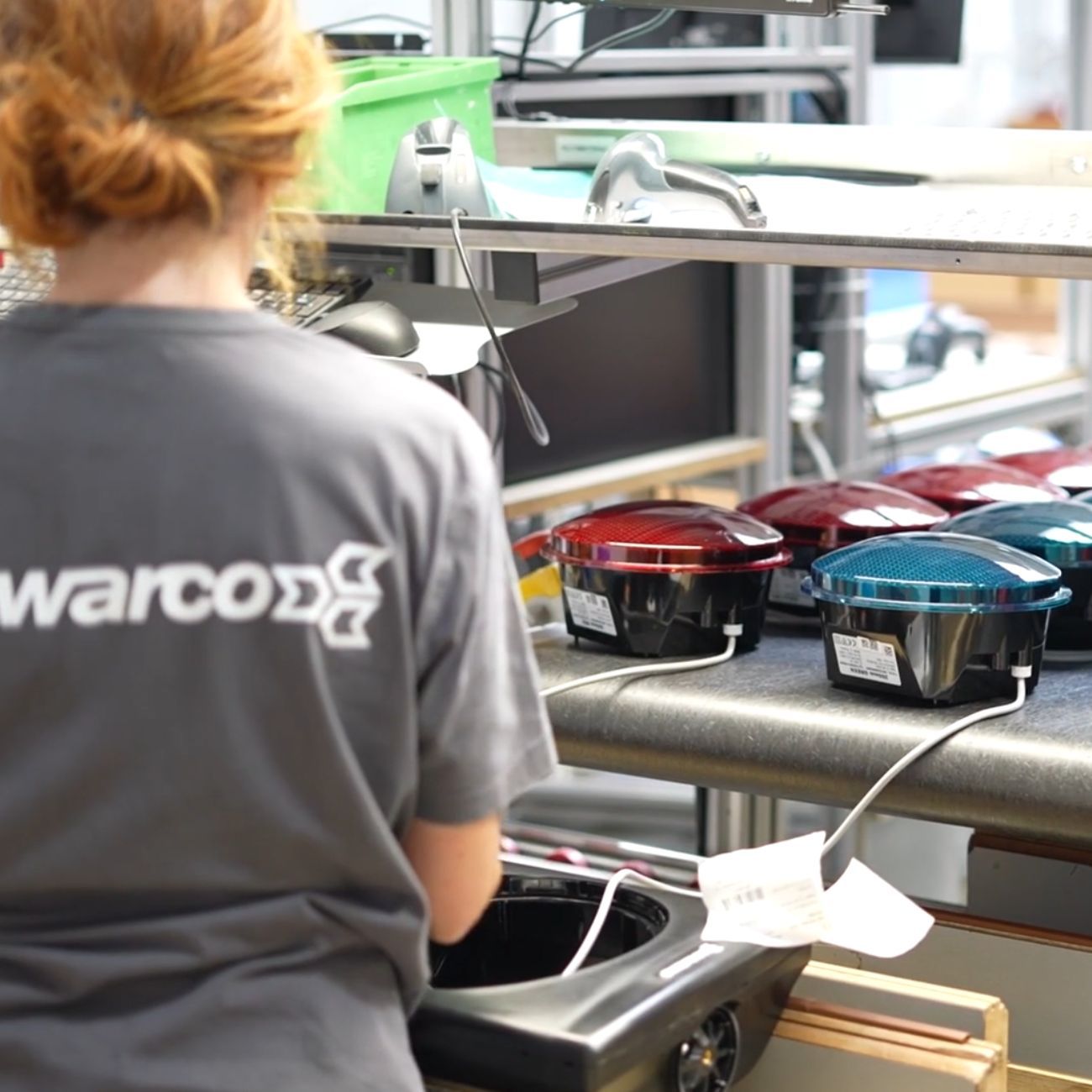
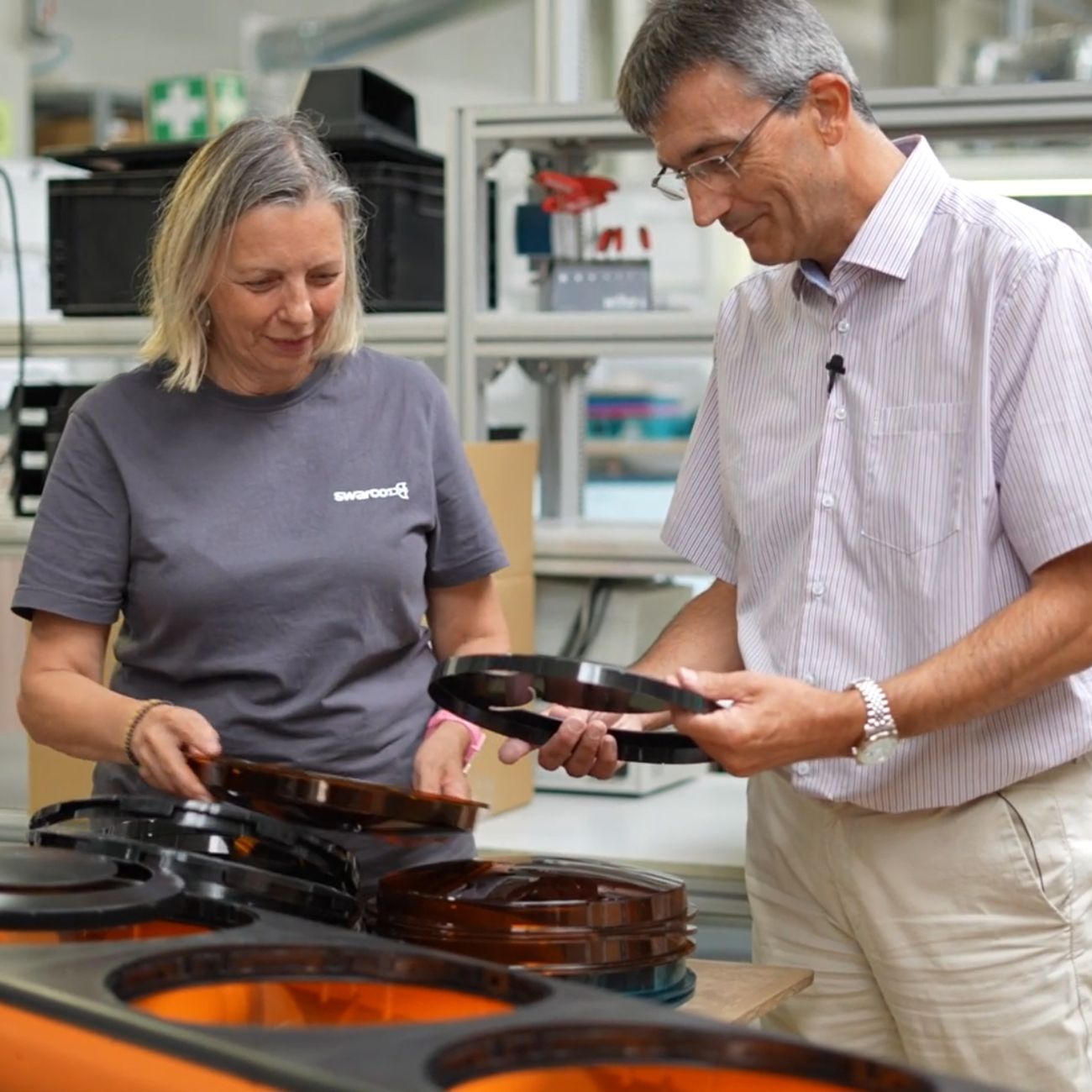